APPLYING ADVANCED TECHNOLOGIES TO CREATE A SAFER WORKPLACE
Greater engagement, enhanced efficiency, more informed decision making when it comes to safety: the dividends of an industry-first project to transform a critical HSE programme.
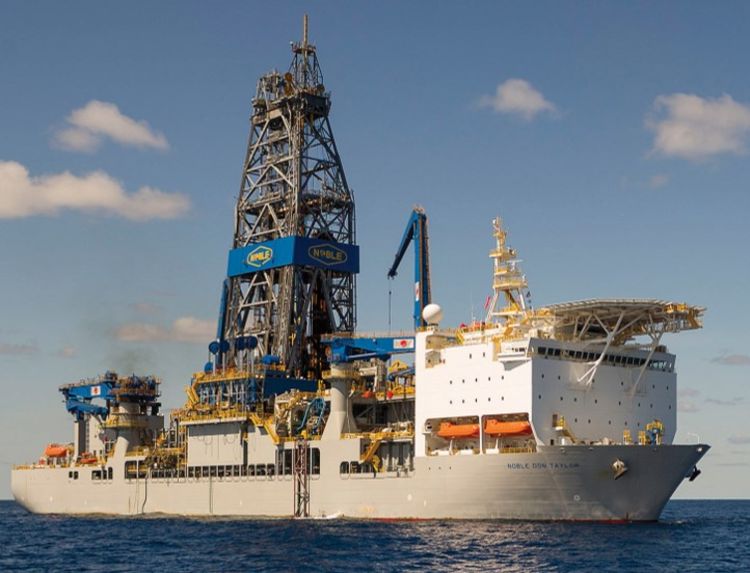
The Challenge
Existing methods to execute behaviour-based safety observation programmes – designed to improve workplace safety by encouraging employees to practice safe behaviour while recognising and mitigating risks – are becoming increasingly burdensome, time-consuming and inefficient.
They rely on data collection using paper cards, with manual entries to generate reports and spreadsheets that are then stored and shared for updates and analysis, turning most safety data trends and insights into lagging indicators.
As the oil & gas industry faces tumultuous challenges, many business leaders are accelerating the adoption of digital technologies to deliver safer, more efficient operations with less environmental impact.
Noble Corporation identified an opportunity to optimise its safety observation programme, but no appropriate solution was readily available. Many digital solutions fail to address industry-specific challenges, and the increasing complexity of risks and safety management processes have made the effective application of data-driven technologies significantly harder.
And for organisations with varying levels of digital readiness across diverse global operations, leaders are more cautious about implementing solutions that are not fit for purpose as they jeopardise the consistency in business process execution at the corporate level.
The Response
In collaboration with Noble's HSE and IT teams, Fennex specialists built a bespoke digital solution with two main areas that were particularly critical for its successful rollout:
- Align with the company data governance requirements, the internal HSE system, and corporate branding.
- In-built capabilities to allow secure and consistent safety observation data reporting using digital and physical entry processes.
The Fennex BBSS™ solution used an intelligent and innovative application of machine learning (ML) and artificial intelligence (AI) technologies, combining safety observation data from digital and physical entry points into a Microsoft Azure environment with the real-time publication of dashboards and customised Power BI reports.
Robotic Process Automation (RPA) was applied to automate routine tasks and workflows, removing complexity, saving time, and maximising clarity. Data entry is secured through a portal to all users from phones, tablets or desktops. By simply scanning a QR code, an observation can be completed within seconds using smart Apps with online and offline capabilities. Smart technology HotSync seamlessly works in the background to ensure business continuity, even with weak or no internet.
In addition, a physical card designed with the company's HSE branding and hazard classifications was then produced. It was used for conversion to digital data at the scanning point, allowing consistent global-scale deployment regardless of digital readiness across the fleet. Cloud-based architecture offers advanced collaboration and real-time insights into critical safety indicators to ensure people's safety
The BBSS™ key features & benefits:
- secure mobile access tools reduce paper use and improve ease of data entry
- full alignment with HSE branding and classification system makes it easy to adopt
- streamlined, efficient and easy to execute
- makes safety observation attractive and accessible, boosting engagement and improving the overall safety culture
- captures, tracks and reports vast amounts of data and analyses safety trends before they become lagging indicators
- connects the field to the boardroom with real-time reports and alerts
- cloud-based architecture offers advanced collaboration and real-time insights into critical safety indicators to ensure people's safety
- improves accountability and compliance, raising employees' skills in risk awareness
- provides evidence and history of compliance.
The Result
- engagement: 30% increase in employee and third-party participation in safety reporting
- speed: Data and analysis enables deeper insights, leading to quicker decision-making to mitigate risks and prevent hazards
- cost: 70% reduction in overall programme costs
- sustainability: 500,000 paper cards are eliminated each year
- efficiency: 15,000 man-hours saved per year through automation of routine tasks, allowing the workforce to focus on high-impact, more critical activities.
‘…. 30% increase in employee and third party participation in safety reporting…70% reduction in overall programme costs… 15,000 man-hours saved per year…’
Find out more: www.fennex.net
Contact: Nassima Brown
Director Marketing Operations
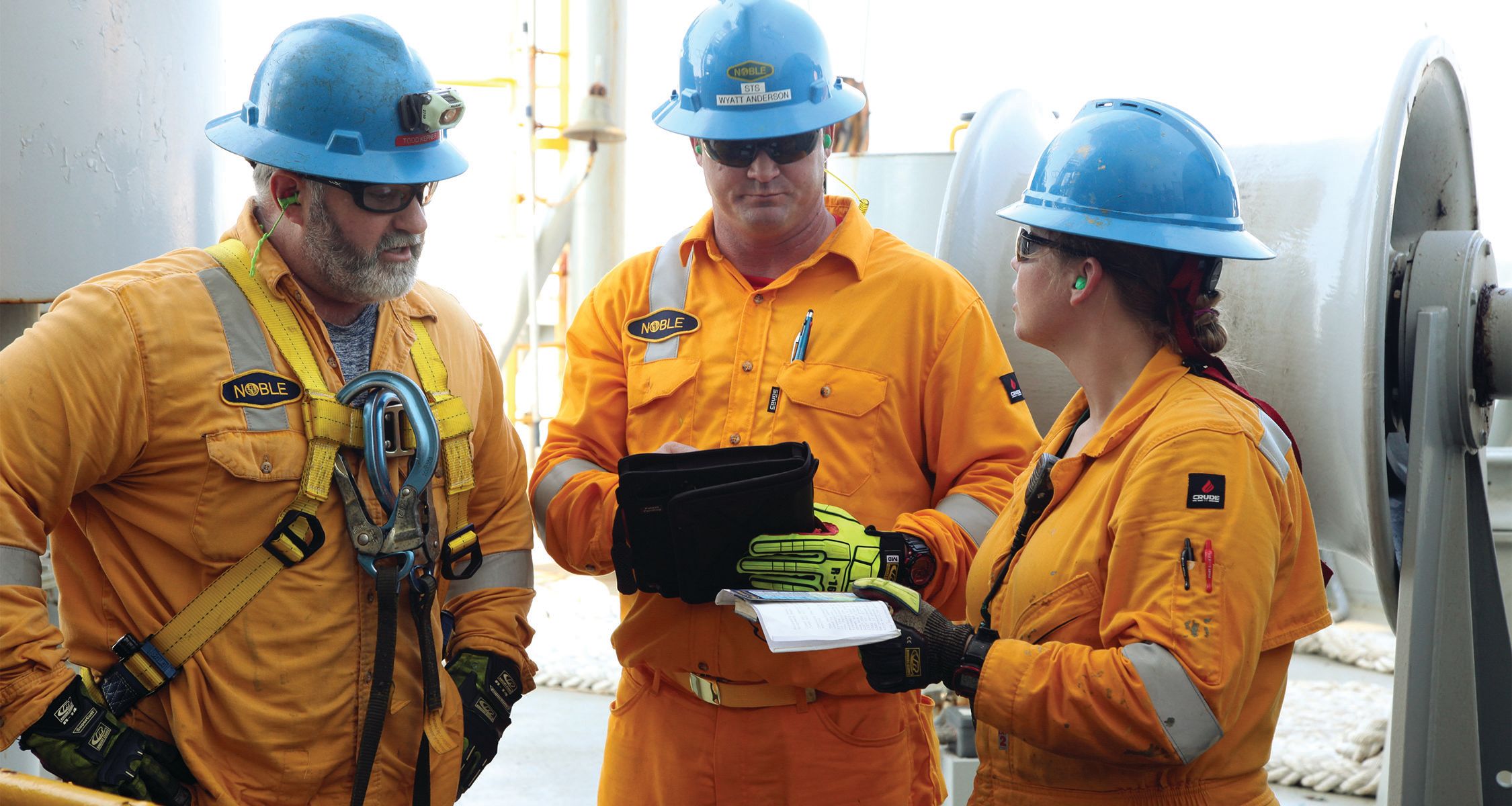
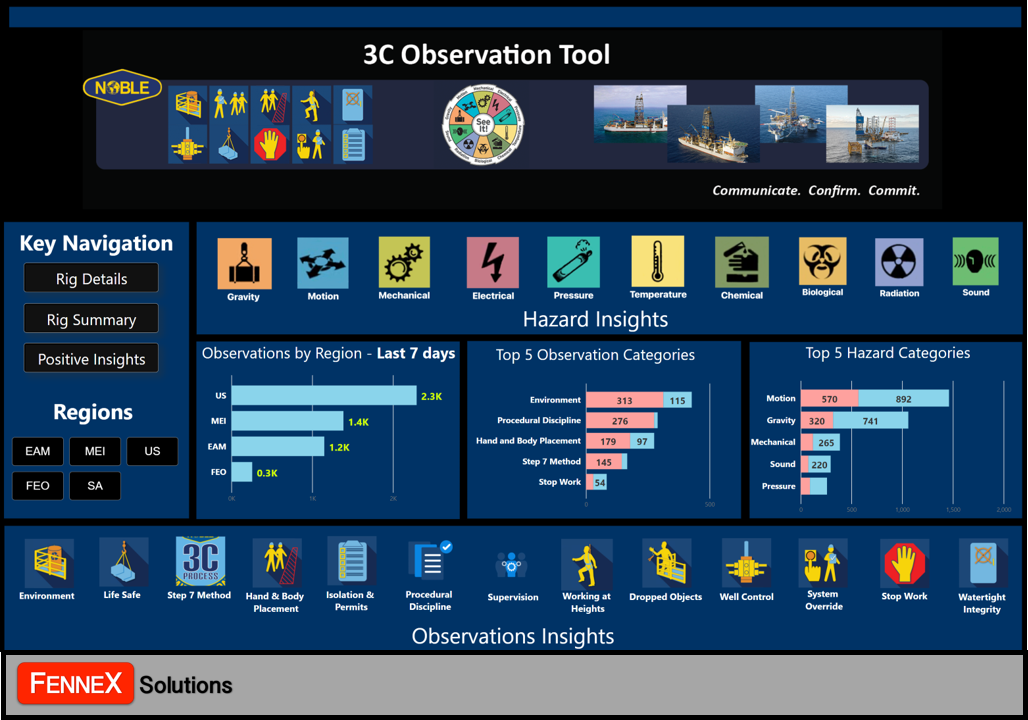
Explore our Case Studies Gallery
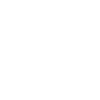
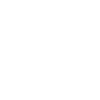