An integrated package: reducing labour when the heat is on
Safer and more efficient ways to provide on-site heat treatment services were put to work on behalf of a major industry player – and the smarter approach realised labour cost savings of 36%.
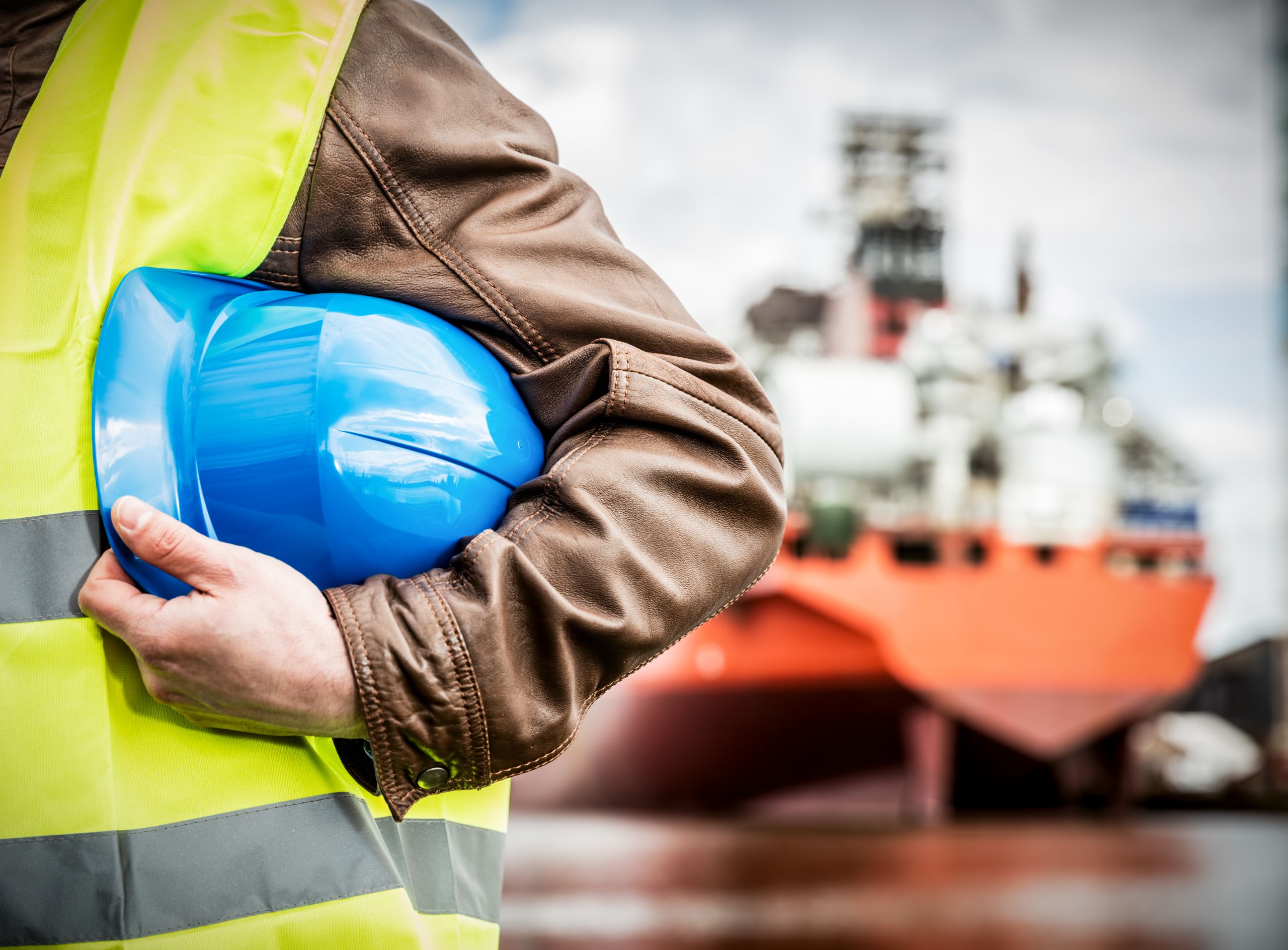
The Challenge
Performing specialist heat treatment services during a refinery-wide turnaround for one of the largest petroleum companies in the UK.
The project had posed major challenges during the planning stages as the client had limited knowledge of the scope due to most of the work being inspection-driven. This complicated the intended work timeline during the turnaround.
The Response
Superheat has integrated emerging communication technology, equipment advances and innovative software solutions to create an industry-leading proposition.
It delivers consistency of control across the heat treatment process through its unique Superheat SmartWay™ approach, which incorporates its new Superheat SmartView™ quality assurance (QA) platform and other technology-led tools.
Superheat applied its suite of solutions to overcome the issues associated with the refinery turnaround.
Implementing its Superheat SmartWrap™ programme, six company supervisors were on site with 24 contracted insulators who completed an extensive pre-turnaround heat treatment course. The combination of training with the Superheat SmartCenter™ remote monitoring and control hub further reduces on-site labour.
The Superheat SmartView™ QA platform – an interactive, web-based tool – was used to upload data such as heat treatment requests, quality and engineering specifications, and IOS drawings. This process improves responsiveness and saves time pre-mobilisation, with most planning taking place in a digital environment. Once the turnaround went live, the client could view the activity status and the estimated start times for jobs being set up for heat treatment. This supported enhanced decision-making as the next steps were planned.
Superheat SmartView™ helped ensure a ''right the first time'' approach to job execution by adding an optional hold point for additional QA inspection. It also ensured QA parameters were adhered to, offering the highest levels of transparency. The client could monitor live heat cycle charts and status updates in real time from any device.
The client could further quantify its heat treatment at the individual weld level by downloading a complete Superheat SmartReports™ package. This solution compiles all activities related to the weld in a single file or in separate files based on client preferences
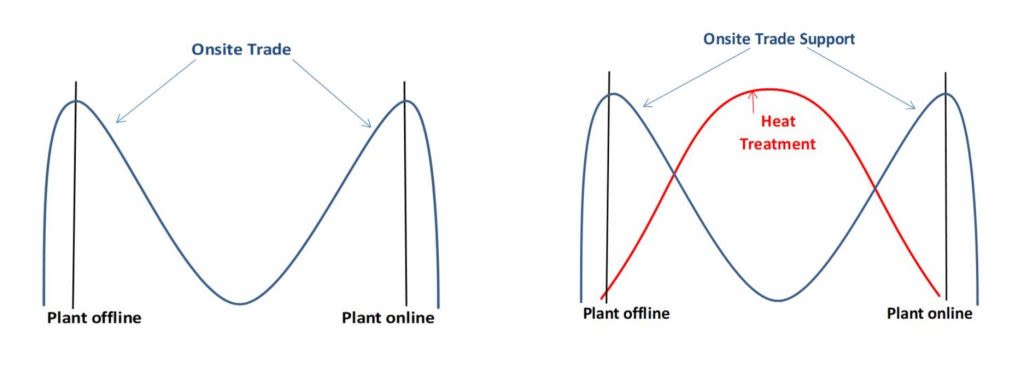
The Result
Superheat'sSuperheat's ability to manage on-site equipment and quality via remote monitoring technology eliminates the need for non-productive equipment monitoring technicians on site. This reduces on-site labour requirements by up to 40% while mitigating safety concerns – specifically the exposure of employees to COVID-19 risks.
In this project, by using contractors on an as-needed basis and capitalising on the advantages of the Superheat SmartView™ platform, the client achieved labour cost savings of 36% overall and reduced the on-site physical footprint to ensure adherence with all COVID-19 legislation.
The adjusted ''wrench time'' for the general insulation contractor on the turnaround was increased by only 3%.
''…reduces on-site labour requirements by up to 40% while mitigating safety concerns – specifically the exposure of employees to COVID-19 risks.''
Find out more: www.superheat.com
Contact: sales@superheat.com or +44 (0)1462 888003
Explore our Case Studies Gallery
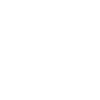
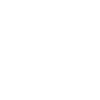